Aluminium Backed PCBs (IMS)
Aluminium backed PCBs are now being used in place of traditional FR4 PCBs for high power LED applications. This is due to rapidly changing developments in LED technology, with brighter more powerful LED’s coming on to the market. This raised a problem to designers with larger amounts of heat being generated by the components, the answer came along on the form of IMS (Insulated Metal Substrate) PCB’s. Aluminium backed PCB’s with the use of thermally conductive pre-preg between the copper and the aluminium the thermal performance is 8–10 times better than a standard epoxy glass (FR4) PCB. We are able to manufacture single sided, PTH or multilayer Aluminium backed PCB’s to your requirements.
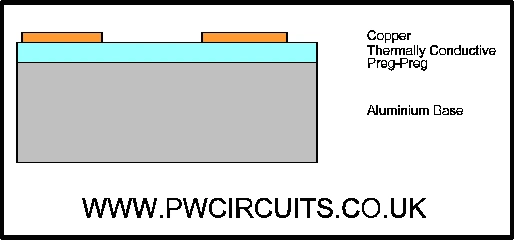
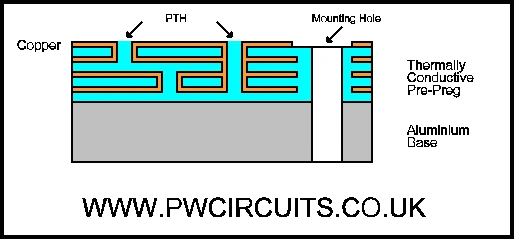
Another common practice with LED application aluminium backed PCBs is the use of White or Black solder resist to reflect light or to help in heat removal. Standard colour solder resist & legend inks can also be applied. A range of surface finishes can be applied, Hot Air Solder Level (HASL) Spb Not RoHS Compliant, Electroless Silver, Electroless Nickel Immersion Gold, Electrolytic Gold (Hard Gold) and OSP (Organic Solderability Preservatives). PW Circuits have invested in two SEL R100 3 axis router’s with customised wet routing features to ensure a burr free profiled aluminium edge.
Contact us today so we can quote all your PCB requirements. Also, check out our YouTube channel for some great PCB content.